How Cross Docking Can Enhance Your Supply Chain Performance
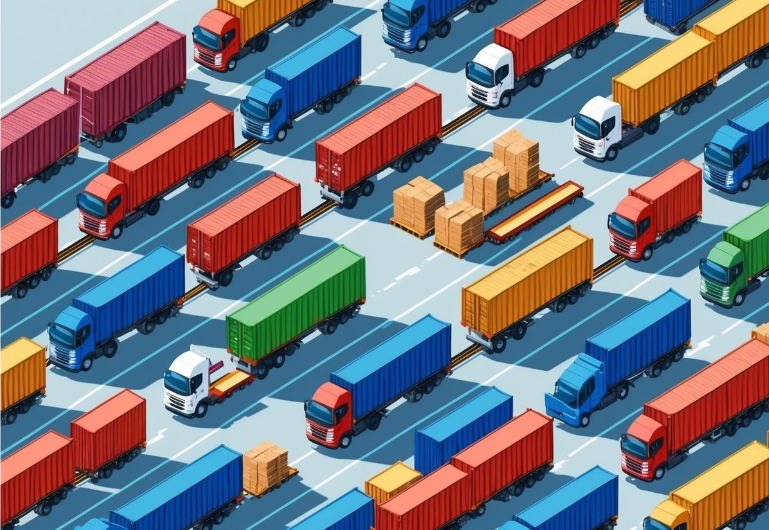
Is your supply chain slowing down your business growth? Cross-docking benefits could be the answer you’re looking for.
This logistics strategy eliminates storage by moving products directly from incoming to outgoing vehicles and cuts handling time and costs. While traditional warehousing ties up your capital in inventory, cross-docking keeps products moving through your supply chain, helps you deliver faster to customers, and has leaner operations.
What is Cross Docking
Let’s break down what cross docking is and how it differs from traditional warehousing methods so you can understand its impact on your supply chain.
What is Cross Docking?
Cross docking is a logistics practice where products from a supplier or manufacturing plant are delivered directly to a customer or retail chain with minimal to no handling or storage time. Instead of storing products in a warehouse, products are unloaded from incoming trucks and loaded onto outgoing trucks, often within 24 hours.
Unlike traditional warehousing, which focuses on storage, cross docking creates a smooth flow of products across the supply chain. In a traditional warehouse, goods sit in storage for days, weeks, or even months before shipping to their final destination. With cross docking, products sit in the distribution center just long enough to be sorted and organized for outbound transportation.
Main Benefits of Cross Docking
One of the biggest benefits of cross-docking is cost reduction. By minimizing or eliminating storage requirements, businesses can reduce warehouse space needs, cutting costs associated with facility maintenance, utilities, and storage equipment. This turns fixed costs into variable costs that scale with your business.
Cross docking also speeds up delivery times. With products in transit and handling for less time, goods get from manufacturer to customer much faster. This is especially valuable for perishable or time-sensitive products that need to get to customers quickly to maintain quality or meet market demands.
Cross Docking vs Traditional Warehousing
Traditional warehousing follows a receive-store-pick-pack-ship model where goods are stored for varying periods. Cross docking follows a streamlined receive-sort-ship process within a shorter timeframe. This difference impacts everything from facility design to staffing and technology needs.
For supply chain managers looking to identify differences between direct distribution and fulfillment services, understanding these operational distinctions is crucial for determining which model best suits specific product categories and business requirements.
Cross docking is ideal for high-volume, fast-moving products with predictable demand. For example, retail chains use cross-docking for core products that sell consistently. Traditional warehousing is better suited for products with unpredictable demand patterns, seasonal products, or products that require special handling or storage conditions.
Cross Docking’s Impact on Supply Chain Performance
Implementing cross-docking can change your supply chain operations in many ways. Here’s how this strategy can improve efficiency and reduce costs across your logistics network.
Speed and Efficiency
Cross docking simplifies the flow of goods by removing unnecessary steps between suppliers and customers. Products move through the supply chain without the delays associated with storage, picking, and packing. This direct transfer approach can reduce handling time by up to 60% compared to traditional warehousing methods.
The reduction in touchpoints has ripple effects throughout the supply chain. Every time a product is handled, there’s a chance of damage, misplacement, or administrative errors. By minimizing these interactions, cross docking not only speeds up delivery but improves accuracy and reduces product damage rates.
Many major retailers have seen significant performance improvements after implementing cross-docking. For example, some retail chains have reported 15-20% faster delivery times and a 25% increase in inventory turns after moving selected product lines to cross-docking operations.
Cost Savings
The cost benefits of cross-docking go beyond simple warehousing cost reduction. By eliminating storage, businesses can operate with smaller facilities focused on sorting and transfer rather than large warehousing. This can reduce facility costs by 25-30% compared to traditional warehousing operations. When combined with techniques like what is zone skipping, businesses can further optimize their logistics network to minimize transit zones and significantly reduce shipping expenses across regional boundaries.
Labor costs are also reduced through cross-docking. With fewer picking, packing, and inventory management tasks, staffing needs decrease while productivity per employee increases. Transportation costs can be optimized through better consolidation and route planning, especially when cross-docking facilities are located to serve multiple markets.
A medium-sized consumer goods company working with specialized logistics partners like Innovative Warehouse Solutions reported annual savings of $250,000 after implementing cross docking for their fast-moving product lines. These savings were mainly from reduced warehousing costs, lower inventory carrying costs, and better transportation utilization.
Customer Satisfaction
In today’s market, customer expectations for fast delivery continue to rise. Cross docking helps businesses meet these demands by reducingthe time products spend in the supply chain. When done correctly cross docking can cut delivery times by 1-3 days compared to traditional warehousing methods, giving you a significant competitive advantage.
The ability to respond quickly to market demand is another customer satisfaction driver. Cross docking facilities can process large volumes of products quickly, allowing businesses to respond faster to sudden demand spikes or distribute new product launches. This responsiveness builds customer trust and loyalty.
Companies that have implemented cross-docking have seen measurable improvements in customer satisfaction metrics. According to data from retailers that have cross-dock buildings, on-time delivery rates improved by 12% and order accuracy by 8% after implementing cross-docking for suitable product lines.
Implementing Cross-Docking in Your Supply Chain
Successful cross-docking integration into your logistics operations requires planning and the right resources. Let’s look at what you need to make cross-docking work for your business.
Infrastructure and Technology
Effective cross-docking needs a specific facility design. The ideal cross-dock building has a rectangular, or I shape with multiple dock doors on opposite sides—inbound shipments come in one side, and outbound shipments go out the other. The facility should have minimal interior obstructions to allow for efficient product movement and sorting.
Technology plays a big part in managing cross-docking operations. A WMS that supports cross-docking functionality is essential for coordinating the movement of goods. This system needs to provide real-time visibility into incoming and outgoing shipments, automate sorting decisions, and assign dock doors.
Modern cross-docking operations are incorporating technologies like barcode scanning, RFID tracking, and automated sorting systems to reduce handling time and improve accuracy. Some advanced systems even use predictive analytics to predict incoming shipment volumes and adjust staffing and resource allocation accordingly.
Strategic Planning and Execution
Implementing cross-docking starts with identifying which products are best suited for this approach. Ideal candidates are high-volume items with predictable demand, products with short shelf life, and pre-packaged items that require minimal handling. Start with a limited product selection to test processes before rolling out to other suitable items.
Cross docking needs to align with your overall supply chain strategy. This includes working with suppliers to ensure product quality and delivery schedules. Many companies have strict vendor compliance programs that specify packaging requirements, labeling standards, and delivery windows to support cross-docking operations.
When evaluating cross-docking rates and adoption timing, consider starting with a pilot program on a single product category or specific high-volume customers. This allows you to refine processes, train staff, and identify potential issues before full-scale implementation.
Partnering with 3PLs for Cross Docking
For many businesses, partnering with a 3PL is the fastest way to implement cross-docking. 3PLs already have the infrastructure, technology, and operational expertise to do cross-docking. This partnership approach eliminates the need for capital investment in facilities and systems.
3PLs that specialize in cross-docking can provide the flexibility and scalability that’s hard to achieve on your own. During peak seasons or promotional periods you can increase your cross docking volume without capacity constraints. During slower periods, you can scale back without maintaining unused infrastructure.
When selecting a 3PL partner for cross docking services, evaluate their experience with similar products and industries. Ask for specific information on their cross dock vs rear load facilities, as the facility design makes a big difference to operational efficiency. Many businesses find that partners who excel at small parcel fulfillment can offer more comprehensive solutions that integrate cross docking with last-mile delivery needs. Other key factors are geographic coverage, technology capabilities and established carrier relationships.
Cross Docking Advantages FAQs
What are the three main types of cross-docking?
The three main types of cross-docking are manufacturing cross-docking, retail cross-docking, and opportunistic cross-docking. Manufacturing cross-docking consolidates raw materials for production. Retail cross-docking moves products directly to stores. Opportunistic cross-docking transfers incoming shipments to outbound trucks without storage.
What is the difference between cross-docking and transloading?
The main difference between cross-docking and transloading is storage and handling. Cross-docking transfers goods directly from inbound to outbound transport with minimal storage time. Transloading involves temporary storage and transferring goods between different transportation modes, such as from rail to truck.
What type of product is most suitable for cross-docking?
Perishable goods, high-demand retail items, and pre-packaged consumer products are most suitable for cross-docking. These items require fast movement through the supply chain to prevent spoilage, meet demand, or reduce storage costs.
What are the risks of cross-docking?
The risks of cross-docking include inventory mismanagement, delays, damaged goods, and high dependency on logistics coordination. Without precise timing and tracking, errors can disrupt operations and increase costs.
What are the challenges of cross-docking?
The main challenges of cross-docking include supply chain synchronization, infrastructure investment, and reliable supplier coordination. Efficient cross-docking requires real-time inventory tracking, skilled labor, and advanced warehouse management systems to prevent bottlenecks.
Conclusion
Cross docking benefits continue to make this logistics strategy attractive for businesses looking to optimise their supply chain. By removing unnecessary storage and handling you can achieve significant cost savings and speed to market and customer satisfaction. The cross docking vs traditional warehousing comparison clearly shows that for the right products and market conditions cross docking is the better option.
As supply chains get more complex and customer demand for fast delivery continues to rise cross docking is a practical solution that answers both operational and market demands. Whether implemented in-house or with a 3PL partner cross docking can turn your logistics into a competitive advantage.
Ready to Try Cross Docking for Your Business?
At Innovative Warehouse Solutions, we specialize in helping businesses implement effective cross docking strategies that deliver measurable supply chain improvement. Our transparent pricing means you’ll always know what you’re paying for, no hidden fees or surprises.
Ready to find out more about cross docking for your business? Contact us today for a consultation. Our logistics experts will help you determine if cross docking is right for your products and develop a customised implementation plan that fits your business goals.