The Essential Guide to Distribution and Fulfillment Center Operations
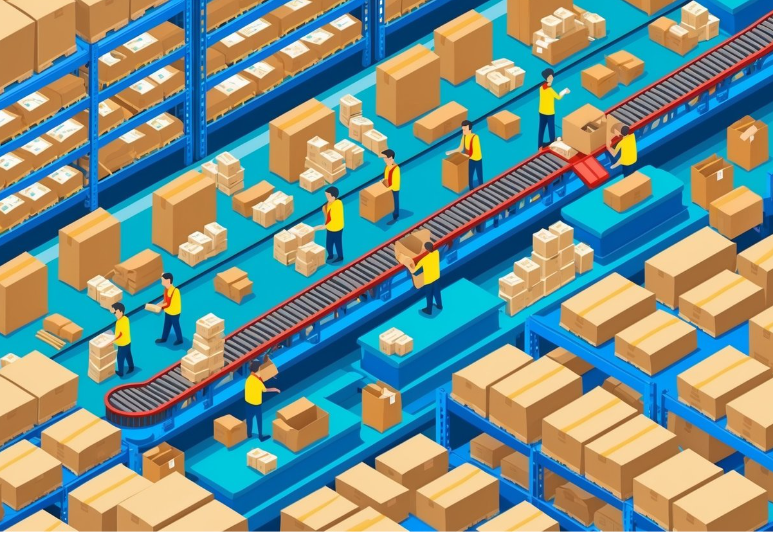
Are your products reaching customers efficiently, or is your supply chain clogging up? To know the difference between direct distribution and fulfillment services, you need to understand their purposes.
Distribution centers move bulk products to retailers, fulfillment centers handle individual customer orders. This difference affects your operational costs, delivery time and customer satisfaction. For growing brands shipping 300+ orders a month, choosing the right logistics approach can mean the difference between growing and chaos.
Distribution Centers vs Fulfillment Centers
Both distribution and fulfillment centers are critical in modern supply chains but operate under different models to achieve different goals.
What is a Distribution Center?
A distribution center is designed to receive, store and redistribute large quantities of products to other businesses, retail locations or secondary distribution points. These centers connect manufacturers with retailers and wholesalers through bulk product movement.
Distribution centers process large shipments and are located in strategic places that minimize transportation costs while having access to major shipping routes. Their operations revolve around space utilization and inventory tracking systems that optimize the movement of palletized goods.
Functions of a Distribution Center
The main focus of a distribution center is the flow of products through the supply chain at scale:
- Receiving and Storage: Distribution centers receive large shipments from manufacturers, usually full truckloads or container quantities. Products are stored in palletized units not individual items.
- Cross-Docking and Redistribution: Many centers move products from inbound to outbound vehicles with minimal storage time, keeping products moving to retailers and wholesalers.
- Advanced Transfer Methods: Many distribution centers utilize the benefits of cross docking to minimize storage time and handling costs. This technique allows products to move directly from inbound to outbound transportation, dramatically reducing warehouse dwell time and accelerating the flow of goods through the supply chain.
- Transportation Optimization: Strategic locations near transportation hubs help minimize lead times while maximizing delivery efficiency, crucial for brands in competitive retail.
What is a Fulfillment Center?
A fulfillment center focuses on processing individual customer orders for direct-to-consumer businesses. While distribution centers connect businesses to businesses, fulfillment centers connect businesses to end consumers through accurate and fast order processing.
Two key characteristics of fulfillment centers are speed and accuracy over long term storage. They process high volumes of small orders, making them perfect for e-commerce businesses. Unlike distribution centers, fulfillment center operations prioritize inventory turnover over storage.
Functions of a Fulfillment Center
The specialized nature of fulfillment centers is evident in their core functions:
- Order Processing: When a customer clicks “buy” integrated systems send that information to the fulfillment center instantly and trigger the fulfillment workflow.
- Picking, Packing, and Shipping: Staff or automated systems locate products, package them for individual shipment and prepare them for delivery with emphasis on accuracy and presentation.
- Returns Management: Fulfillment centers handle return processing, inspection, restocking and refunds – a critical service for customer satisfaction.
- Specialized Handling: Modern fulfillment centers excel at small parcel fulfillment for direct-to-consumer brands, with expertise in packaging individual items safely and cost-effectively regardless of size or fragility. This specialization is particularly valuable for businesses with diverse product catalogs or those selling items requiring special handling.
Distribution and Fulfillment Services Comparison
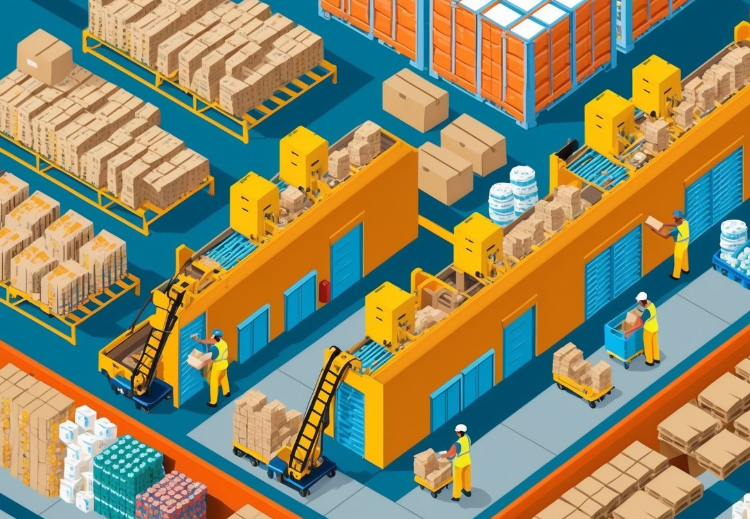
Understanding the operational differences between these two logistics models helps businesses make informed decisions about their supply chain.
Direct Distribution vs Fulfillment Services
Direct distribution and fulfillment services are two different ways to get products to their destination. The key differences lie in the level of control, operational involvement and target recipients.
In direct distribution businesses have more control over the entire process from warehouse operations to transportation logistics. This is typically company owned or contracted facilities moving products to retail locations or other businesses. The focus is on bulk movement and inventory positioning.
Fulfillment services on the other hand specialize in individual customer orders, often as a third-party provider. These services excel in processing many small orders not few large shipments. For e-commerce businesses partnering with a fulfillment service like Innovative Warehouse Solutions allows them to focus on product development and marketing while leaving the operational logistics to experts.
Operational and Logistical Differences
The operational structures of these two models reveal significant contrasts in how they function:
Aspect | Direct Distribution | Fulfillment Services |
Control | Complete control over logistics operations including staffing, equipment, and transportation | Operations managed by third-party experts with limited direct oversight |
Flexibility | More standardized operations year-round with less ability to scale quickly | Easily scales during peak seasons without requiring additional infrastructure investment |
Technology Focus | Emphasis on inventory tracking and route optimization for bulk shipments | Priority on order management systems integrated with e-commerce platforms and real-time consumer updates |
Order Types | Primarily handles large, bulk shipments to businesses | Specializes in processing numerous small individual orders |
Geographic Reach | Limited by company-owned facility locations | Access to established network of fulfillment centers for broader coverage |
Advantages and Disadvantages
Each approach offers distinct benefits and challenges that businesses should consider when developing their logistics strategy.
Direct Distribution | Fulfillment Services | |
Advantages | Direct distribution provides greater control over brand presentation and customer experience. Companies can potentially achieve higher margins by eliminating third-party costs. This model also offers direct access to distribution data and insights, along with the ability to customize operations for specific product requirements. | Fulfillment services require reduced capital expenditure through transparent, pay-for-what-you-use pricing models. Businesses gain access to established logistics networks and expertise without building their own. This approach offers the ability to scale operations quickly during growth periods, while allowing companies to focus resources on creating products and generating sales rather than managing logistics. |
Disadvantages | This approach requires significant capital investment in facilities, equipment, and personnel. It involves complex logistics management requiring specialized expertise that may distract from core business growth. Direct distribution offers less flexibility during seasonal fluctuations and creates geographic limitations based on facility locations. | Fulfillment services provide less direct control over fulfillment operations, which may create consistency challenges. Some providers lack transparency in their pricing and performance metrics. Companies may face challenges with accommodating complex product requirements unless they choose a partner experienced in their specific industry. |
Future of Distribution and Fulfillment
The landscape is changing driven by technological innovation and consumer expectations. Understanding the trends helps businesses prepare for what’s next.
Technology
Technology is impacting both distribution and fulfillment:
- Automation and Robotics: Warehouse automation is changing picking, packing and sorting processes. Mobile robots and automated storage systems increase efficiency and reduce labor costs, allowing industry leaders to maintain accuracy even during peak volume.
- Artificial Intelligence and Predictive Analytics: Smart systems optimize inventory levels, anticipate demand fluctuations and identify potential supply chain disruptions before they happen. This proactive approach keeps inventory balanced and prevents stockouts.
- Integration: Modern fulfillment centers offer seamless integration with e-commerce platforms like Shopify, WooCommerce and Amazon. These connections eliminate manual order processing and provide real-time inventory visibility across all sales channels.
- Last Mile: New approaches to final delivery include micro-fulfillment centers in urban areas and strategic regional placement to reduce shipping costs and delivery times. These solutions address the most expensive part of the delivery process.
- Order Status Transparency: Modern fulfillment systems provide customers with detailed tracking information throughout the delivery process. Understanding terms like pending remote fulfillment helps both businesses and consumers track order status accurately and predict delivery timeframes, leading to improved customer communication and satisfaction.
Sustainability
Environmental concerns are reshaping logistics across both distribution and fulfillment:
- Green Facility Design: Modern logistics facilities are incorporating sustainable features like energy efficient systems and water conservation measures. These reduce environmental impact and often lower operational costs.2. Packaging: Sustainable packaging reduces waste and protects products during transit. Right-sized packaging, biodegradable materials and reusable containers make for more eco-friendly fulfillment.
- Transportation: Route optimization, vehicle efficiency and load consolidation reduce carbon emissions in product movement. Good for the planet and the bottom line.
- Circular Supply Chains: Advanced returns processing creates circular supply chains where products and materials stay in circulation through multiple lifecycles. This requires sophisticated tracking and processing.
Direct Distribution and Fulfillment Services FAQs
What is the difference between direct distribution and indirect distribution?
The main difference between direct and indirect distribution is intermediaries. Direct distribution sells products straight to consumers without third parties, while indirect distribution uses wholesalers, retailers, or distributors to reach customers. Direct distribution offers more control and higher profits, but indirect distribution provides wider market reach.
What is the difference between fulfillment and logistics?
Fulfillment focuses on processing and delivering customer orders, including storage, packing, and shipping. Logistics involves broader supply chain management, covering transportation, warehousing, and inventory control. Fulfillment is a part of logistics, ensuring efficient order handling and customer satisfaction.
What is the difference between a fulfillment center and a warehouse?
A fulfillment center processes and ships customer orders quickly, handling inventory storage, picking, packing, and shipping. A warehouse primarily stores goods for long periods without actively handling order processing. Fulfillment centers focus on speed and efficiency, while warehouses prioritize bulk storage.
What is the difference between fulfillment service and dropshipping?
A fulfillment service stores, packs, and ships products for businesses that own inventory. Dropshipping allows retailers to sell products without holding inventory, with suppliers shipping orders directly to customers. Fulfillment services require inventory investment, while dropshipping eliminates upfront stock costs.
What is the difference between direct to consumer and dropshipping?
Direct-to-consumer (DTC) brands sell products directly to customers, managing inventory and fulfillment. Dropshipping relies on third-party suppliers to handle inventory and shipping. DTC offers better brand control and higher margins, while dropshipping minimizes risk but reduces control over product quality and delivery.
Conclusion
The decision between direct distribution and fulfillment services is a strategic one with big implications for your business growth. Distribution centers are great at moving bulk quantities to businesses, fulfillment centers are expert at processing individual orders for end consumers.
For most businesses shipping 300+ orders a month, the best approach depends on your specific needs, resources and growth stage. Many successful companies use hybrid models, direct distribution for certain channels and fulfillment services for e-commerce.
As technology evolves and consumer expectations change, both distribution and fulfillment must adapt. The winning logistics strategies will be automated, transparent and customer centric.
Ready to transform your logistics? Contact Innovative Warehouse Solutions today to talk about how our transparent, customer focused fulfillment services can help your business grow and simplify operations.