Drinks Logistics: Streamlining 3PL Solutions for the Food and Beverage Industry
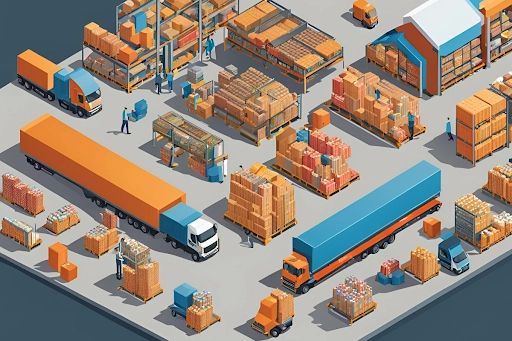
Managing drinks logistics in-house is a resource drain and holds back your business growth. As volumes grow, maintaining temperature control, tracking stock and compliance gets more and more complicated. Small to medium-sized drinks businesses find themselves stuck between rising customer expectations and operational limitations. That’s where specialist 3PL support turns your supply chain headaches into growth opportunities.
What is Specialist Drinks Logistics
Storing and distributing drinks requires more than basic shipping services. Food and drink logistics needs temperature control, specialist handling, and inventory management. Many brands see their teams overwhelmed trying to balance these requirements with growing customer demand.
Product quality suffers when businesses try to do everything in-house. Partnering with experienced 3PL drinks logistics specialists gives you access to proven processes, trained staff, and specialist facilities. A qualified partner has deep knowledge of safety protocols, regulations, and tracking systems to protect your products and brand.
Challenges in Drinks Logistics and Solutions
Temperature Control and Product Protection
Maintaining proper temperature throughout storage and shipping directly impacts product quality and shelf life. Professional 3PL providers use monitoring systems in their facilities and delivery vehicles to maintain optimal conditions.
Innovative Warehouse Solutions provides dedicated cold storage and temperature tracking, with immediate notification systems for any variations. Special care is particularly important for glass containers – our team follows industry-leading practices for how to ship glass bottles of liquid to ensure they arrive safely at their destination.
Proper handling prevents damage during movement and storage. Staff trained in beverage-specific protocols ensure products receive appropriate care at every stage. This careful attention protects brand reputation while reducing losses from mishandled inventory.
Compliance and Quality Control
For drinks businesses, meeting industry standards and FDA requirements is critical. A skilled 3PL partner handles compliance responsibilities, taking the operational burden off you. Their teams are up to date with regulations, perform regular audits, and maintain detailed records to support quality standards.
Inventory Management
Growing businesses need visibility into stock levels and order status. IWS offers real-time tracking through easy-to-use software that gives you complete stock transparency. This visibility prevents stock outs, improves order processing, and gives you the data to make informed business decisions.
Partnering with a 3PL: What to Expect
Choosing the right logistics partner is key to business growth. Businesses should look for experience in drink handling, robust technology, and, most importantly – responsive customer service. The assessment should include facility inspection, equipment review, and scalability.
Quality partnerships deliver more than just storage and shipping. IWS offers:
- Temperature-controlled storage tailored to your product
- Accurate order processing
- Packaging options
- Transparent pricing
- Real-time inventory tracking
- Dedicated customer service support
Growing Through Efficient Operations
Small to medium-sized drinks brands need flexible packaging solutions. IWS combines storage and packaging services to simplify product preparation and distribution. This integration speeds up order processing while maintaining quality standards. The packaging team follows product-specific protocols to ensure consistent presentation and meet safety and regulatory requirements.
End-to-End Supply Chain Solutions
Products go to many destinations – retail stores to direct customer deliveries. IWS manages the whole distribution process, adapting to each channel’s requirements. System updates give real-time information on order status and stock levels so you can make confident distribution decisions.
Drinks Logistics FAQs
What is the difference between logistics and third-party logistics?
The main difference between logistics and third-party logistics (3PL) is control. Logistics refers to the internal management of transportation, warehousing, and distribution. 3PL involves outsourcing these services to external providers for improved efficiency and scalability.
How are soft drinks transported?
Soft drinks are transported in temperature-controlled trucks or containers to prevent spoilage. Bottles and cans are packed in shrink-wrapped pallets for stability. Bulk shipments may use food-grade tankers for syrup transport before bottling.
What are the 3 types of logistics?
The three main types of logistics are inbound logistics, outbound logistics, and reverse logistics. Inbound logistics manages supply chain sourcing, outbound logistics handles product distribution, and reverse logistics deals with returns and recycling.
What are the protocols for liquid handling?
Liquid handling protocols include using sealed containers, maintaining proper temperature control, following hazardous material guidelines when necessary, and ensuring secure transportation to prevent leaks or contamination. Regulatory compliance depends on the type of liquid being transported.
Your Drinks Logistics Partner
IWS is different in the drinks industry because of our personal service. Unlike big, faceless logistics providers, our dedicated customer service team gets back to you quickly. Each client gets regular updates and direct access to the support team for any questions or special requests.
We structure our services around your business growth. From our transparent pricing to our flexible storage options, we make logistics management easy and efficient. We focus on providing reliable and transparent service so you can focus on growing your business.
To learn how we can help streamline your beverage logistics operations, contact us to discuss your specific needs and goals.